Compressed Air Requirements
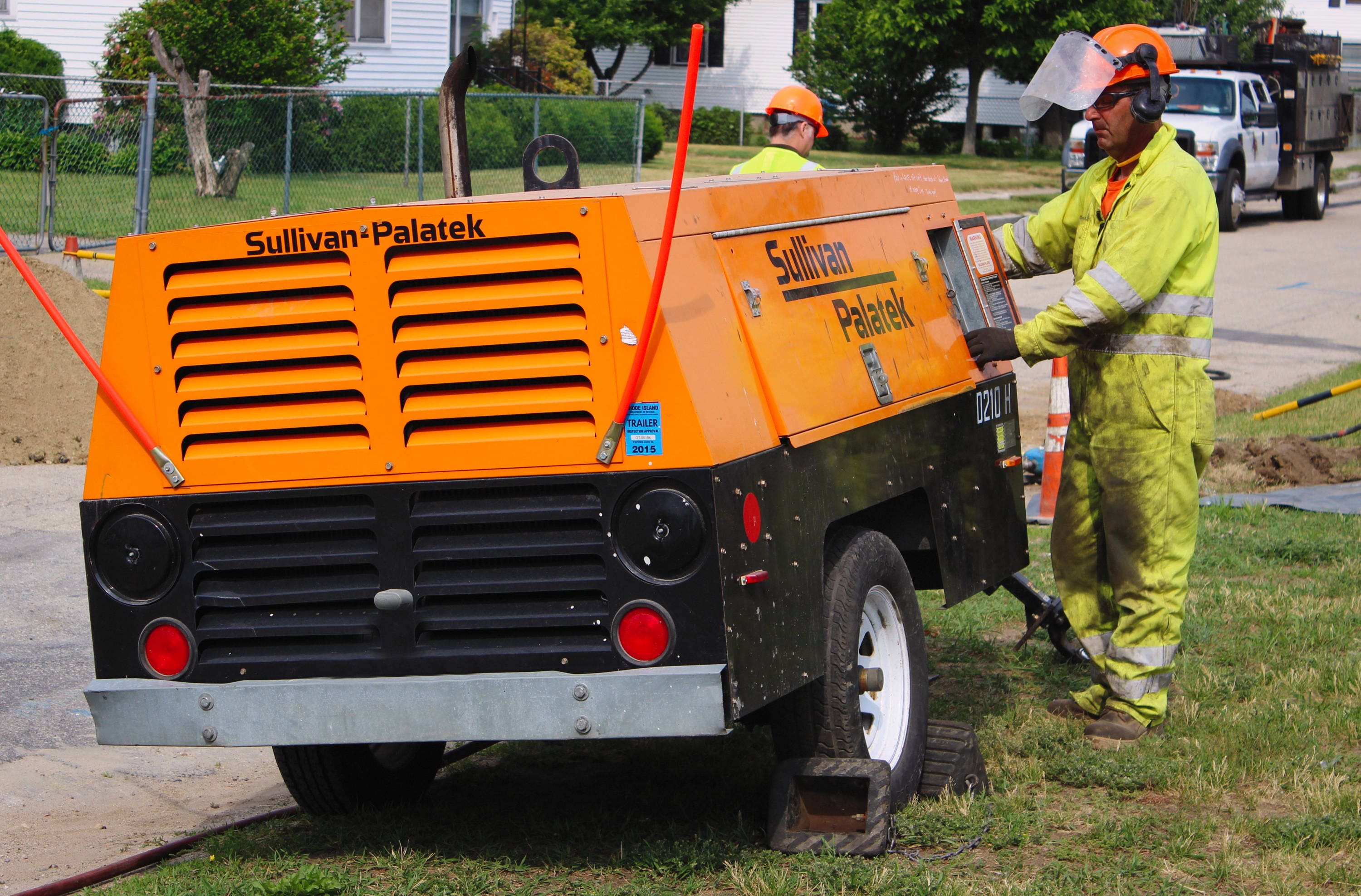

Compressor Size
Air compressors are sized by air pressure and air flow. In the US, pressure is measured in pounds per square inch (psi). Flow is measured in cubic feet of air per minute (cfm). Virtually all air compressors nominally operate at approximately 100 psi while air flow capacities vary from model to model, from a few cfm for small electric piston units to hundreds of cfm for gas or diesel driven portable screw compressors.
All AirSpade nozzles are designed to operate optimally at 90 psi and are manufactured in six different sizes (air flow rates) to match standard, commercially available compressors (see table below). Note that a smaller nozzle may always be used on a larger capacity compressor, but not the reverse. Running a nozzle with a higher flow rating than the capacity of the compressor will result in a significant pressure drop (less than 90 psi at the nozzle) and will noticeably diminish performance.
POPULAR PRODUCTS
LEARN MORE ABOUT AIRSPADE
AirSpade Supersonic Nozzle
Supersonic nozzle turns compressed air into a high-speed, laser-like jet...
Benefits of Air Excavation
Air excavation has become a preferred method for digging on many jobs...
Digging with AirSpade
AirSpade is effective in virtually all soils and even hard clays...
Soil Characteristics
Although hundreds of different types of soils exist...
AirSpade Recommended Compressor Size
Model
Nozzle Size (cfm)
Recommended Compressor Size (cfm)*

2000
25
60
105
150
225
25 - 30
60 - 70
125
175 - 185
250

3000
330
375

4000
105
150
125
175 - 185
@90 psi
Air Pressure
All AirSpade supersonic nozzles are designed to operate at 90 psi in order to produce a Mach 2 air-jet. Since the vast majority of portable air compressors deliver compressed air in the 90 to 100 psi range to run standard air tools, the AirSpade is well matched to most compressors.
Increasing the air pressure above 90 psi delivered to the supersonic nozzle does not lead to a proportional gain in excavation capability. For example, increasing the compressor output pressure (by say 20%) increases the air-jet force and exit momentum flux (stress seen by the soil) but only nominally. Supplying higher pressure to a supersonic nozzle designed to work at 90 psi actually de-focuses the air-jet thereby degrading the performance. In addition, the energy required to operate the compressor at higher pressures increases dramatically due to increased fuel consumption.
Air Hose Size
Compressed air flowing through an air hose experiences a loss in pressure from friction and constrictions. Friction loss is proportional to the length of the hose. Operating pressure, flow rate, air hose inner diameter, and air hose smoothness also determine the loss. The table below shows the pressure loss for 50 feet of common air hose (including couplings) as a function of air hose size and air flow (nozzle size).
Pressure Loss (psi) for 50 Feet of Common Air Hose*
Model
Air Flow (cfm)
Air Hose (ID)
3/4"
1"
1 1/4"

2000
25
60
105
150
225
0.3
1.6
5.6
12.2
29.9
0.1
0.5
1.2
2.9
8.0
0.0
0.1
0.4
0.8
1.9

3000
330
64.6
20.1
4.4

4000
105
150
5.6
12.2
1.3
2.9
0.4
0.8
* @90 psi
The above table can be interpreted with the following example. Assume an AirSpade equipped with a 150 cfm supersonic nozzle connected to an air compressor via a 50 ft long, ¾" ID air hose. From the table, the air hose will see a 12.2 psi pressure loss over its length. In order to deliver 90 psi at the supersonic nozzle (for optimal performance), ideally the compressor output should be set at 102.2 psi (90 + 12.2) to make up for the pressure loss.
Alternatively, with the same AirSpade and compressor, a 1" ID air hose will see a 2.8 psi pressure loss over its length. Thus the compressor should be set at 92.8 psi (90 + 2.8), a negligible increase. Consequently, to minimize pressure loss, matching 1" ID air hose with AirSpade 2000, and 1-1/4" ID air hose with AirSpade 3000, is recommended.
Connectors and Fittings
Be sure that connectors and fittings do not restrict the air flow in any manner. Use fittings that are rated the same size, or larger, for a given air hose size. AirSpade recommends the use of Chicago "Air King" style fittings, used in conjunction with safety pins.